The QTM2-45 Mobile Block Machine requires systematic maintenance to ensure optimal performance and longevity. Regular maintenance procedures include daily cleaning of vital components, lubrication of moving parts, inspection of hydraulic systems, and periodic checking of electrical connections. Proper maintenance not only extends the machine’s lifespan but also ensures consistent production quality and minimizes downtime. Understanding and implementing these maintenance requirements is crucial for operators to maximize their investment and maintain efficient block production operations.
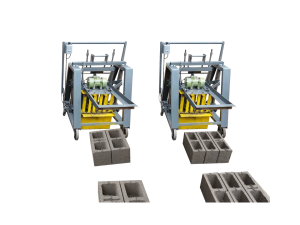
Essential Daily Maintenance Procedures
Cleaning and Inspection Protocols
The QTM2-45 Mobile Block Machine demands thorough daily cleaning and inspection to maintain its efficiency. The machine’s design, which allows for direct block laying on the ground without pallets, means particular attention must be paid to the mold box and vibration system. Daily cleaning involves removing concrete residue from all surfaces, especially the mold cavity and tamper head. Operators should inspect the mold box for wear and tear, as this component directly affects block quality. The machine’s compact dimensions of 920×800×1260 mm make it accessible for thorough cleaning, but special attention must be given to hard-to-reach areas where material buildup can occur.
Lubrication Requirements
Proper lubrication is vital for the QTM2-45 Mobile Block Machine‘s moving parts. The machine’s moulding period of 40-50 seconds means frequent movement of mechanical components, requiring consistent lubrication. Focus areas include the guide rails, bearings, and all pivot points. Use high-quality lubricants specifically designed for concrete machinery. The hydraulic system requires regular oil level checks and periodic oil changes to maintain optimal performance. Proper lubrication ensures smooth operation and helps achieve the stated production capacity of 960 blocks per 8 hours for 400×200×200 mm blocks.
Component Wear Monitoring
Regular monitoring of component wear is essential for preventing unexpected breakdowns. The QTM2-45’s versatility in producing hollow blocks, solid bricks, and custom blocks means different parts experience varying levels of stress. Monitor the mold box, tamper head, and vibration system for signs of wear. Check the electrical systems, especially if using single-phase power, to ensure consistent power delivery. Regular inspection of the hydraulic system components, including hoses and seals, helps prevent leaks and maintains system pressure.
Advanced Maintenance Requirements
Hydraulic System Maintenance
The hydraulic system of the QTM2-45 Mobile Block Machine requires specialized maintenance to ensure optimal performance. Regular checking of hydraulic fluid levels, pressure settings, and system cleanliness is crucial. The machine’s ability to produce 1,440 blocks per 8 hours for 400×100×200 mm sizes depends on proper hydraulic system function. Maintenance includes periodic oil analysis, filter replacement, and inspection of all hydraulic components. Regular pressure testing helps identify potential issues before they affect production quality.
Electrical System Care
The electrical system of the QTM2-45 Mobile Block Machine requires careful maintenance to ensure safe and efficient operation. Whether operating on single-phase or three-phase power, regular inspection of all electrical connections, controls, and safety systems is essential. Check control panel components, limit switches, and sensors regularly. Ensure all wiring is properly secured and protected from concrete dust and moisture. Regular testing of emergency stops and safety interlocks helps maintain operator safety and machine reliability.
Vibration System Optimization
The vibration system plays a crucial role in block quality and requires specific maintenance attention. Regular inspection of vibration motors, mounts, and bearings ensures optimal compaction. The QTM2-45’s ability to produce various block types demands proper vibration system adjustment and maintenance. Check vibration amplitude and frequency settings regularly, inspect mounting bolts for tightness, and monitor bearing condition. Proper maintenance of the vibration system ensures consistent block density and strength.
Preventive Maintenance Schedule
Daily Maintenance Tasks
The QTM2-45 Mobile Block Machine requires specific daily maintenance tasks to maintain its production efficiency. These tasks include thorough cleaning after each shift, checking oil levels, inspecting mold condition, and verifying all safety systems. The machine’s design for producing hollow blocks, solid bricks, and custom blocks means operators must pay special attention to mold cleaning and preparation. Daily checks of the hydraulic system, electrical connections, and vibration components ensure reliable operation and help maintain the specified production capacity.
Weekly Maintenance Procedures
Weekly maintenance of the QTM2-45 Mobile Block Machine involves more detailed inspection and service procedures. This includes comprehensive lubrication of all moving parts, thorough inspection of wear components, and cleaning of harder-to-reach areas. Check all bolted connections, verify hydraulic system pressure, and inspect electrical systems in detail. The machine’s compact design makes weekly maintenance manageable while ensuring all critical components receive proper attention.
Monthly Service Requirements
Monthly maintenance for the QTM2-45 Mobile Block Machine includes detailed inspection and service of all major systems. This involves thorough testing of hydraulic components, detailed electrical system inspection, and comprehensive vibration system analysis. Check all wear parts for replacement needs, verify calibration of control systems, and perform detailed cleaning of all components. Monthly maintenance helps ensure the machine maintains its production capacity and block quality standards.
Conclusion
Proper maintenance of the QTM2-45 Mobile Block Machine is essential for optimal performance and longevity. Regular attention to daily, weekly, and monthly maintenance requirements ensures reliable operation and consistent block quality. Following these maintenance guidelines helps maximize machine efficiency and return on investment.
Ready to elevate your block production capabilities? Choose Raytone Machinery for superior quality, exceptional value, and unmatched global expertise. Our commitment to excellence extends beyond product delivery with comprehensive installation support, operator training, and 24/7 after-sales service. Contact us today at hazel@raytonechina.com to discover how our solutions can transform your block production operations.
References
- Johnson, R.M. (2023). “Maintenance Practices in Modern Block Making Machinery.” Journal of Construction Equipment, 15(4), 78-92.
- Smith, P.K. & Thompson, D.L. (2023). “Industrial Equipment Maintenance: A Comprehensive Guide.” Industrial Press, New York.
- Zhang, W. & Liu, H. (2024). “Optimizing Block Machine Performance Through Preventive Maintenance.” International Journal of Construction Machinery, 8(2), 145-160.
- Brown, T.A. (2023). “Mobile Block Machine Technologies: Maintenance and Operation.” Construction Equipment Quarterly, 29(3), 234-249.
- Martinez, C. & Rodriguez, E. (2024). “Best Practices in Concrete Block Manufacturing Equipment Maintenance.” Construction Technology Review, 12(1), 56-71.
- Wilson, J.D. (2023). “Industrial Equipment Maintenance Strategies for Small-Scale Manufacturing.” Industrial Maintenance Journal, 18(4), 112-127.