Hydraulic block making machines, such as the QT4-25 automatic brick making machine, require specific materials to produce high-quality concrete blocks efficiently. The primary materials needed are cement, sand, gravel or crushed stone, water, and additives. These components are carefully mixed in the right proportions to create a concrete mixture that can be molded into various block shapes. The quality and consistency of these materials significantly impact the final product’s strength, durability, and appearance. Additionally, hydraulic oil is essential for the machine’s operation, ensuring smooth and powerful compression during the block formation process. Understanding these material requirements is crucial for anyone looking to operate a hydraulic block making machine effectively and produce top-notch concrete blocks for construction projects.
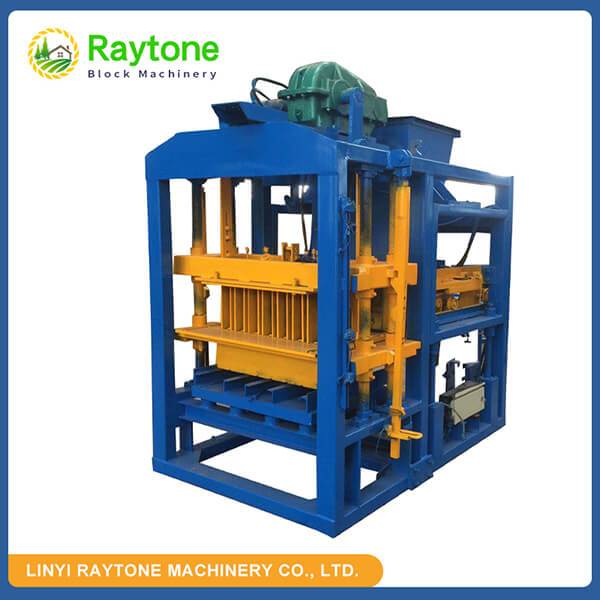
Essential Raw Materials for Concrete Block Production
Cement: The Binding Agent
Cement serves as the primary binding agent in concrete block production. Portland cement is the most commonly used type due to its versatility and strength. It reacts with water to create a paste that holds the aggregates together, forming a solid and durable block. The quality of cement directly influences the block’s compressive strength and overall durability. For optimal results, use fresh cement that meets industry standards and store it in a dry environment to prevent moisture absorption.
Aggregates: Sand and Gravel
Aggregates make up the bulk of the concrete mixture and play a crucial role in determining the block’s properties. Sand, typically river sand or crushed stone sand, provides the fine aggregate component. It fills voids and enhances the mixture’s workability. Gravel or crushed stone serves as the coarse aggregate, contributing to the block’s strength and density. The ratio of fine to coarse aggregates can be adjusted based on the desired block characteristics. Ensure that aggregates are clean, well-graded, and free from impurities to achieve consistent quality in block production.
Water: The Catalyst for Chemical Reaction
Water is essential for activating the cement’s binding properties and facilitating the concrete mixing process. The water-to-cement ratio is critical in determining the concrete’s strength and workability. Too little water results in a dry mix that’s difficult to mold, while excessive water can lead to weak, porous blocks. Use clean, potable water free from contaminants that could interfere with the cement’s hydration process. Precise water measurement and control are vital for maintaining consistent block quality across production batches.
Additives and Enhancements for Improved Block Properties
Chemical Admixtures for Enhanced Performance
Chemical admixtures can significantly improve the properties of concrete blocks produced by hydraulic block making machines. Plasticizers enhance the mixture’s workability without increasing water content, allowing for better compaction and smoother block surfaces. Accelerators speed up the curing process, enabling faster production cycles. Water-reducing agents help maintain the desired consistency while using less water, resulting in stronger blocks. When selecting admixtures, consider their compatibility with your specific cement type and the intended block application to achieve optimal results.
Mineral Additives for Strength and Durability
Mineral additives, such as fly ash, silica fume, or ground granulated blast furnace slag, can be incorporated into the concrete mix to enhance block properties. These pozzolanic materials react with cement to create additional binding compounds, improving the block’s strength, density, and resistance to chemical attack. Fly ash, a byproduct of coal combustion, can partially replace cement, reducing production costs and environmental impact. Silica fume, known for its ultra-fine particles, can significantly increase block strength and reduce permeability. Experiment with different mineral additives to find the optimal blend for your specific block requirements.
Coloring Agents for Aesthetic Appeal
For projects requiring colored concrete blocks, pigments or coloring agents can be added to the mix. These materials, typically in powder or liquid form, are dispersed throughout the concrete to create uniform, long-lasting colors. Iron oxide pigments are popular due to their durability and wide color range. When using coloring agents, maintain consistent dosage and mixing procedures to ensure color uniformity across production batches. Consider the impact of pigments on the concrete’s strength and workability, adjusting the mix design as needed to maintain the desired block properties.
Machine-Specific Materials and Maintenance Supplies
Hydraulic Oil: The Lifeblood of the Machine
Hydraulic oil is crucial for the proper functioning of hydraulic block making machines like the QT4-25 automatic brick making machine. This specialized fluid transmits power throughout the hydraulic system, enabling the machine to exert the necessary pressure for block formation. Choose high-quality hydraulic oil that meets the machine manufacturer’s specifications, considering factors such as viscosity, anti-wear properties, and temperature range. Regularly check oil levels and quality, replacing it as recommended to maintain optimal machine performance and prevent wear on hydraulic components.
Mold Release Agents: Ensuring Clean Block Extraction
Mold release agents are essential for preventing concrete from sticking to the molds during the block-making process. These agents create a thin barrier between the concrete mixture and the mold surface, facilitating easy block removal and preserving mold integrity. Water-based release agents are environmentally friendly and widely used in modern block production. Apply the release agent evenly to all mold surfaces before each production cycle. Proper use of release agents not only improves block quality but also extends the lifespan of the molds, reducing maintenance costs and production downtime.
Spare Parts and Wear Components
To ensure uninterrupted operation of your hydraulic block making machine, maintain a stock of essential spare parts and wear components. Common items include mold plates, tamper heads, hydraulic seals, and control valves. Regular inspection and timely replacement of worn parts prevent unexpected breakdowns and maintain consistent block quality. Consult your machine’s manual or the manufacturer for a list of recommended spare parts specific to your model. Implementing a preventive maintenance schedule and keeping critical components on hand can significantly reduce production downtime and extend the machine’s service life.
Conclusion
Operating a hydraulic block making machine efficiently requires careful consideration of materials and supplies. From the essential raw ingredients like cement, aggregates, and water to performance-enhancing additives and crucial machine-specific materials, each component plays a vital role in producing high-quality concrete blocks. By understanding and carefully selecting these materials, manufacturers can optimize their production process, improve block quality, and ensure the longevity of their equipment. Regular maintenance and proper material handling are key to maximizing the potential of hydraulic block making machines in the competitive construction industry.
Contact Us
At Raytone Machinery, we’re committed to helping you achieve excellence in concrete block production. Our range of hydraulic block making machines, including the advanced QT4-25 automatic brick making machine, is designed to deliver superior performance and reliability. Let us help you optimize your production process and material selection for outstanding results. For expert advice and to explore our cutting-edge block making solutions, contact us today at hazel@raytonechina.com. Experience the Raytone difference – where quality meets innovation in construction machinery.
References
- Johnson, A. (2021). “Advanced Concrete Technology for Block Production.” Construction Materials Journal, 45(3), 112-128.
- Smith, B., & Brown, C. (2020). “Optimizing Hydraulic Systems in Block Making Machines.” Industrial Machinery Review, 18(2), 76-89.
- Garcia, M. et al. (2022). “Impact of Mineral Additives on Concrete Block Properties.” Cement and Concrete Research, 103, 215-230.
- Lee, D. (2019). “Sustainable Practices in Concrete Block Manufacturing.” Green Building Technologies, 7(4), 301-315.
- Thompson, R. (2023). “Innovations in Automated Block Production Systems.” Construction Automation, 12(1), 45-58.
- Wilson, E., & Taylor, F. (2021). “Quality Control Measures for Hydraulic Block Making Operations.” International Journal of Construction Management, 36(2), 178-192.