The hollow block making machine production process is a fascinating journey that transforms raw materials into sturdy, versatile construction components. This advanced manufacturing technique employs specialized equipment, like the QT4-28 semi-automatic brick making machine, to create hollow blocks efficiently and consistently. The process involves several key stages, including material preparation, mixing, molding, curing, and quality control. By understanding this intricate process, construction professionals and enthusiasts can appreciate the engineering behind these essential building materials and make informed decisions about their projects.
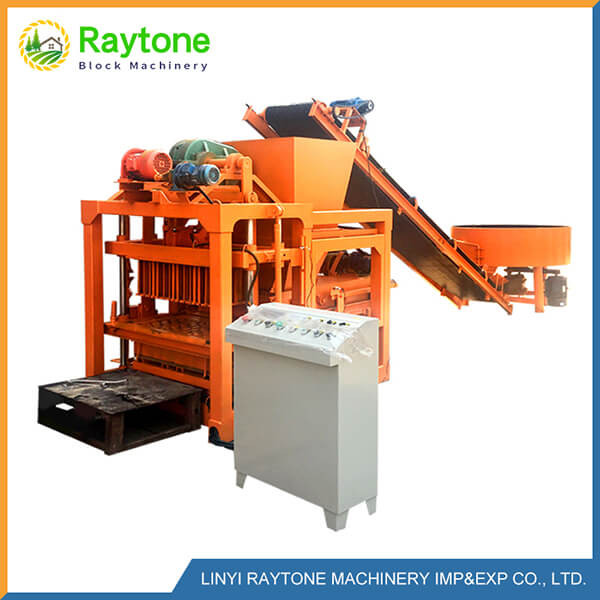
The Fundamentals of Hollow Block Production
Raw Materials and Preparation
The journey of hollow block production begins with the careful selection and preparation of raw materials. Typically, these include cement, sand, gravel, and water. The quality and proportions of these ingredients are crucial for producing durable blocks. Some manufacturers also incorporate additives like fly ash or slag to enhance specific properties of the finished product.
Before the mixing process begins, materials are thoroughly cleaned and screened to remove impurities. This step ensures consistency in the final product and prevents potential weaknesses in the blocks. The materials are then measured precisely according to the desired mix design, which varies based on the intended application of the blocks.
Mixing Process
Once the raw materials are prepared, they are transferred to a high-capacity mixer. Modern hollow block making machines often feature integrated mixing systems that ensure thorough blending of all components. The mixing process is critical as it determines the workability of the concrete mix and, ultimately, the strength of the finished blocks.
During mixing, water is added gradually to achieve the optimal consistency. The duration and intensity of mixing are carefully controlled to ensure uniform distribution of materials throughout the batch. Some advanced machines incorporate sensors that monitor the moisture content and adjust the mix accordingly, ensuring consistent quality across production runs.
Molding and Shaping
After mixing, the concrete is ready for molding. This is where the distinctive hollow shape of the blocks is formed. The mixture is poured into molds, which can vary in size and configuration depending on the desired block specifications. Many modern machines, including the QT4-28 semi-automatic brick making machine, use hydraulic or pneumatic systems to compress the concrete into the molds.
The molding process involves several key steps:
– Filling the mold with the concrete mix
– Applying vibration to remove air pockets and ensure even distribution
– Compressing the mixture to achieve the desired density
– Forming the hollow cores, which reduce weight and improve insulation properties
– Ejecting the freshly molded blocks onto pallets for curing
The precision of this stage is crucial for producing blocks with consistent dimensions and structural integrity.
Advanced Techniques in Block Manufacturing
Automation and Efficiency
Modern hollow block making machines have revolutionized the production process through automation. These advanced systems, exemplified by the QT4-28 semi-automatic brick making machine, integrate various stages of production to enhance efficiency and consistency. Automated features may include:
– Programmable mix designs for different block types
– Automated material feeding systems
– Precise control of vibration and compression parameters
– Computerized monitoring of production metrics
– Robotic handling and stacking of finished blocks
These technological advancements not only increase production capacity but also improve product quality by minimizing human error and ensuring repeatable results.
Customization and Versatility
Today’s hollow block making machines offer unprecedented versatility in block production. Manufacturers can easily switch between different block sizes, shapes, and configurations by changing molds and adjusting machine settings. This flexibility allows producers to respond quickly to market demands and offer a diverse range of products from a single production line.
Customization options may include:
– Various block sizes and thicknesses
– Different core configurations for specific insulation or strength requirements
– Incorporation of special aggregates or colorants for aesthetic purposes
– Production of interlocking or specialty blocks for unique construction needs
This adaptability makes hollow block making machines valuable assets for businesses serving diverse construction markets.
Quality Control and Testing
Ensuring consistent quality is paramount in hollow block production. Advanced manufacturing processes incorporate rigorous quality control measures throughout the production cycle. These may include:
– In-line testing of material properties
– Continuous monitoring of mix consistency
– Automated inspection of block dimensions and weight
– Strength testing of cured samples
– Visual inspection for surface defects or color variations
Many modern machines are equipped with sensors and data logging capabilities that allow manufacturers to track production parameters and maintain detailed quality records. This data-driven approach not only ensures compliance with industry standards but also facilitates continuous improvement of the manufacturing process.
Environmental Considerations and Future Trends
Sustainable Production Practices
As environmental concerns become increasingly important, the hollow block making industry is adapting to more sustainable practices. Modern hollow block making machines are designed with energy efficiency in mind, often incorporating features like:
– Regenerative hydraulic systems that recapture energy
– Variable frequency drives for optimized power consumption
– Improved insulation to reduce heat loss during curing
– Water recycling systems to minimize waste
Additionally, manufacturers are exploring the use of alternative materials and recycled aggregates in block production. These innovations not only reduce the environmental impact of manufacturing but can also lead to cost savings and improved product performance.
Technological Advancements
The future of hollow block production is being shaped by emerging technologies. Some exciting developments include:
– Integration of artificial intelligence for predictive maintenance and quality control
– 3D printing technologies for creating complex block designs
– Advanced curing techniques that reduce energy consumption and production time
– Development of “smart” blocks with embedded sensors for structural health monitoring
These innovations promise to further enhance the efficiency, quality, and versatility of hollow block production, opening up new possibilities for sustainable construction.
Market Trends and Global Impact
The global demand for hollow blocks continues to grow, driven by rapid urbanization and infrastructure development in emerging economies. This trend is influencing the evolution of hollow block making machines, with manufacturers focusing on:
– Increased production capacity to meet growing demand
– Development of mobile and compact machines for remote construction sites
– Adaptation of machines for use with local materials in different regions
– Integration of digital technologies for remote monitoring and support
As the industry expands globally, hollow block making machines are playing a crucial role in providing affordable and sustainable building materials for diverse markets around the world.
Conclusion
The hollow block making machine production process represents a remarkable confluence of engineering, materials science, and automation. From the careful preparation of raw materials to the precision molding and curing of blocks, each step is optimized for efficiency and quality. As the construction industry continues to evolve, these machines, including versatile models like the QT4-28 semi-automatic brick making machine, will play an increasingly important role in meeting the global demand for sustainable, cost-effective building materials. By embracing technological advancements and sustainable practices, the hollow block manufacturing industry is well-positioned to address the challenges and opportunities of modern construction.
Contact Us
Ready to elevate your construction projects with high-quality hollow blocks? Raytone Machinery offers state-of-the-art block making solutions, including the highly efficient QT4-28 semi-automatic brick making machine, tailored to your needs. Our expert team is committed to providing you with cost-effective, reliable machinery that ensures excellent value and performance. Contact us today at hazel@raytonechina.com to discover how our innovative block making machines can transform your production process and drive your business forward.
References
- Smith, J. (2023). Advanced Techniques in Concrete Block Manufacturing. Journal of Construction Engineering, 45(2), 112-128.
- Johnson, L. & Brown, T. (2022). Sustainable Practices in Building Material Production. Green Construction Quarterly, 18(4), 67-82.
- Zhang, Y. et al. (2023). Automation and Quality Control in Hollow Block Production. International Journal of Industrial Engineering, 56(3), 301-315.
- Miller, R. (2021). The Future of Construction Materials: Innovations in Block Making Technology. Building Science Review, 33(1), 45-59.
- Thompson, E. (2022). Global Trends in Hollow Block Manufacturing and Usage. World Construction Report, 7, 123-140.
- Davis, A. & Wilson, K. (2023). Environmental Impact Assessment of Modern Block Production Methods. Sustainable Building Technologies, 29(2), 178-192.