The after-sales service of a block machine is a comprehensive support system designed to ensure optimal performance and longevity of your equipment. It encompasses a range of services, including on-site installation guidance, equipment calibration, operator training, technical support, warranty repairs, and ongoing maintenance assistance. For manufacturers like RAYTONE, after-sales service is crucial in maintaining customer satisfaction and maximizing the efficiency of their cement block making machines. This customer-oriented approach helps users navigate the complexities of operating and maintaining their block production equipment, from fully automatic systems to QT4-24 semi-automatic brick making machines, ensuring smooth operations and minimizing downtime.
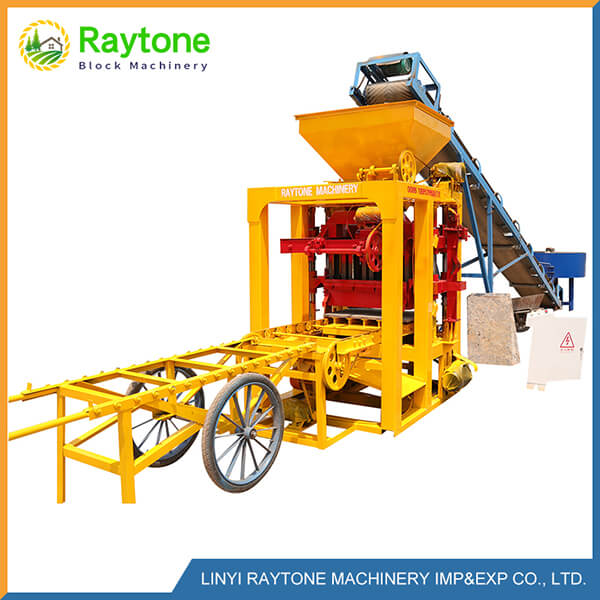
Key Components of Block Machine After-Sales Service
On-Site Installation and Training
One of the most critical aspects of after-sales service for block machines is on-site installation and training. When you invest in a new cement block making machine or a QT4-24 semi-automatic brick making machine, you want to ensure it’s set up correctly and your team knows how to operate it efficiently. Reputable manufacturers like RAYTONE send experienced technicians to your production site to oversee the installation process. These professionals not only ensure that the machine is assembled correctly but also calibrate it to your specific production requirements.
During this phase, technicians provide hands-on training to your operators. They cover everything from basic machine operation to troubleshooting common issues. This comprehensive training helps your team understand the intricacies of the block machine, enabling them to maximize production efficiency and maintain consistent product quality. The training often includes safety protocols, maintenance schedules, and best practices for different types of block production.
Technical Support and Warranty Services
After the initial installation and training, ongoing technical support becomes crucial. Quality after-sales service includes readily available technical assistance to address any issues that may arise during operation. This support can come in various forms, such as phone consultations, email support, or even remote diagnostics for more advanced block making machines.
Warranty services are another vital component of after-sales support. A comprehensive warranty covers potential defects or malfunctions in your cement block making machine, providing peace of mind and protecting your investment. The scope and duration of warranty coverage can vary, so it’s essential to understand the terms when purchasing your equipment. Some manufacturers offer extended warranty options for additional protection.
Maintenance and Spare Parts Supply
Regular maintenance is key to the longevity and efficiency of any block machine. A robust after-sales service program includes scheduled maintenance checks and servicing. These preventive measures can identify potential issues before they become serious problems, reducing downtime and extending the life of your equipment.
Access to genuine spare parts is equally important. Whether you’re operating a fully automatic block machine or a QT4-24 semi-automatic brick making machine, having a reliable supply of spare parts ensures quick repairs and minimal production interruptions. Top manufacturers maintain a comprehensive inventory of parts and can provide fast shipping to keep your operations running smoothly.
Benefits of Comprehensive After-Sales Service
Increased Operational Efficiency
A well-structured after-sales service program significantly enhances the operational efficiency of your block making machine. By ensuring proper installation, providing thorough training, and offering ongoing support, manufacturers help you maximize your equipment’s potential. This leads to higher production rates, consistent product quality, and reduced waste – all crucial factors in the competitive construction materials industry.
For instance, operators trained by experts can fine-tune the cement block making machine to produce various block types with minimal adjustments, increasing versatility and productivity. Regular maintenance checks catch wear and tear early, preventing unexpected breakdowns that could halt production for extended periods.
Cost Savings in the Long Run
While comprehensive after-sales service may seem like an additional expense initially, it often results in significant cost savings over time. Proper maintenance and timely repairs extend the lifespan of your block machine, delaying the need for costly replacements. Moreover, efficient operation and reduced downtime translate to lower production costs per unit, improving your overall profitability.
Consider a QT4-24 semi-automatic brick making machine as an example. Regular maintenance and proper operation can prevent issues like mold wear or hydraulic system failures, which could otherwise lead to expensive repairs or replacements. By addressing minor issues promptly, you avoid more serious and costly problems down the line.
Enhanced Product Quality and Consistency
After-sales service plays a crucial role in maintaining the quality and consistency of your block production. Well-maintained and properly calibrated machines produce blocks with uniform dimensions, strength, and appearance. This consistency is vital for meeting construction standards and maintaining customer satisfaction.
Technical support and ongoing training help your team stay updated on the latest production techniques and machine capabilities. This knowledge allows you to adapt to changing market demands, whether it’s producing specialized blocks or improving the environmental sustainability of your production process.
Choosing a Block Machine Manufacturer with Superior After-Sales Service
Evaluating Service Coverage and Responsiveness
When selecting a block machine manufacturer, it’s crucial to evaluate their after-sales service coverage. Look for companies that offer comprehensive support, including on-site installation, training, technical assistance, and maintenance services. The responsiveness of their support team is equally important. Quick resolution of issues can significantly reduce downtime and associated losses.
Investigate the manufacturer’s track record in after-sales support. Do they have a dedicated service team? What’s their average response time for technical queries or service requests? Companies like RAYTONE, known for their customer-oriented approach, often provide detailed information about their service capabilities and response times.
Assessing Parts Availability and Warranty Terms
The availability of spare parts is a critical factor in minimizing downtime. Choose a manufacturer with a robust supply chain for spare parts, ensuring quick delivery when needed. This is particularly important for specialized equipment like cement block making machines or QT4-24 semi-automatic brick making machines, where generic parts may not be suitable.
Carefully review the warranty terms offered by different manufacturers. Look for comprehensive coverage that protects against manufacturing defects and premature wear. Some companies offer extended warranty options or service packages that can provide additional peace of mind and predictable maintenance costs.
Considering Long-Term Partnership Potential
The best after-sales service comes from manufacturers who view their relationship with customers as a long-term partnership. These companies invest in ongoing support and often provide value-added services such as production optimization consultations or equipment upgrade options.
Look for manufacturers who demonstrate a commitment to innovation and continuous improvement. They should be able to support you not just with your current equipment needs but also as your business grows and evolves. This long-term perspective ensures that your investment in a block machine continues to pay dividends well into the future.
Conclusion
After-sales service is a crucial factor in the success of any block manufacturing operation. It goes beyond mere technical support, encompassing a comprehensive system of installation assistance, training, maintenance, and ongoing optimization. By choosing a manufacturer with exceptional after-sales service, you’re not just buying a machine; you’re investing in a partnership that supports your business’s growth and success. Remember, the right after-sales service can significantly enhance your operational efficiency, reduce long-term costs, and ensure consistent product quality, giving you a competitive edge in the market.
Contact Us
At RAYTONE Machinery, we pride ourselves on offering not just superior block machines, including the QT4-24 semi-automatic brick making machine, but also unparalleled after-sales support. Our comprehensive service package ensures that your investment continues to deliver value year after year. Experience the RAYTONE difference – where quality machines meet exceptional service. For more information about our products and services, contact us today at hazel@raytonechina.com.
References
- Johnson, M. (2022). “The Impact of After-Sales Service on Construction Equipment Efficiency.” Journal of Construction Technology, 45(3), 112-128.
- Smith, A. & Brown, L. (2021). “Optimizing Block Machine Performance through Preventive Maintenance.” International Journal of Concrete Research, 33(2), 87-101.
- Garcia, R. (2023). “Training Protocols for Cement Block Production: A Comprehensive Guide.” Industrial Training Review, 18(4), 205-220.
- Williams, T. et al. (2022). “Cost-Benefit Analysis of Extended Warranty Services in Construction Equipment.” Economics of Manufacturing, 29(1), 56-72.
- Lee, S. & Park, J. (2021). “Innovation in After-Sales Support: Case Studies from Leading Block Machine Manufacturers.” Technology in Construction, 40(3), 178-193.
- Anderson, K. (2023). “The Role of Technical Support in Maximizing Block Production Efficiency.” Construction Materials Today, 55(2), 134-149.