Block machines are essential equipment in the construction industry, used to manufacture concrete blocks efficiently. The materials used in block machines play a crucial role in their performance, durability, and overall quality of the produced blocks. High-quality block machines, such as the automatic block making machine and QT8-15 automatic brick making machine, are constructed using carefully selected materials to ensure longevity and optimal functionality. The primary materials used in block machines include high-strength steel, electric motors with copper wiring, robust hydraulic systems, and advanced PLC control panels.
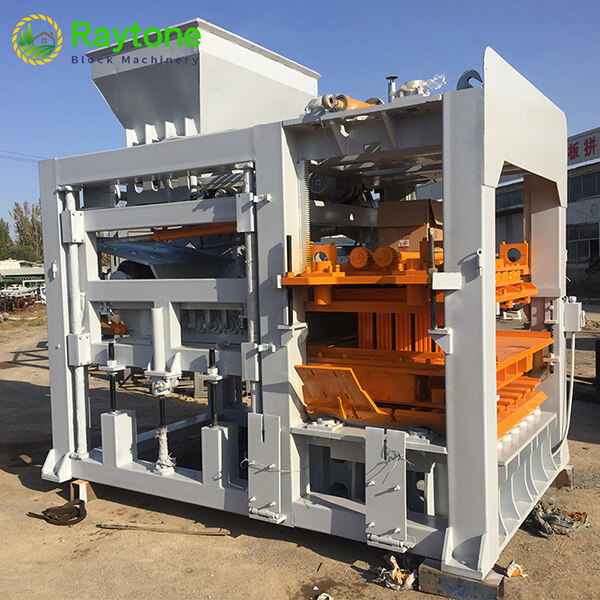
Key Components and Materials in Block Machines
High-Strength Steel: The Foundation of Durability
The backbone of any reliable block machine is high-strength steel. This material is chosen for its exceptional durability and ability to withstand the immense pressure and vibration inherent in the block-making process. The block mould, in particular, requires steel of the highest quality to maintain its shape and integrity over countless production cycles. Manufacturers like Raytone Machinery prioritize the use of premium-grade steel in their automatic block making machines to ensure long-lasting performance and consistent block quality.
Electric Motors: Powering Precision and Efficiency
Electric motors are the driving force behind automatic block making machines, responsible for powering various components and ensuring smooth operation. Quality block machines utilize motors with copper wiring that adhere to national standards. These motors are designed to withstand voltage fluctuations, which is particularly important in regions where power supply may be unstable. The incorporation of high-grade electric motors in machines like the QT8-15 automatic brick making machine contributes to enhanced durability and consistent performance, even under challenging conditions.
Hydraulic Systems: Ensuring Smooth Operation
The hydraulic system is a critical component in block machines, responsible for applying the necessary pressure during the block formation process. Leading manufacturers source hydraulic parts from renowned global brands, including pumps and valves. This commitment to quality ensures that the hydraulic system operates efficiently and reliably, minimizing downtime and maintenance requirements. The integration of top-tier hydraulic components is a hallmark of superior automatic block making machines, contributing to their overall performance and longevity.
Advanced Control Systems and Electrical Components
PLC Control Panels: The Brain of the Operation
Modern block machines rely on sophisticated Programmable Logic Controller (PLC) systems to manage and optimize the production process. These control panels are equipped with high-quality electrical components, including breakers, switches, relays, and adaptors. The use of reputable brands for these critical parts ensures reliable operation and contributes to the overall lifespan of the machine. Advanced PLC systems in automatic block making machines allow for precise control over various parameters, resulting in consistent block quality and improved production efficiency.
Sensors and Monitoring Equipment
To maintain optimal performance, automatic block making machines incorporate various sensors and monitoring equipment. These components are typically made from durable materials capable of withstanding the harsh environment of a block production facility. Sensors play a crucial role in monitoring factors such as pressure, temperature, and material flow, allowing for real-time adjustments and quality control. The integration of high-quality sensors in machines like the QT8-15 automatic brick making machine contributes to enhanced product consistency and reduced waste.
Wiring and Electrical Insulation
The electrical system of a block machine requires robust wiring and insulation to ensure safe and reliable operation. Manufacturers use high-grade copper wiring with appropriate insulation materials to prevent short circuits and electrical failures. This attention to detail in the electrical components is essential for maintaining the longevity of the machine and ensuring operator safety. Quality wiring and insulation are particularly important in automatic block making machines, where complex electrical systems control various aspects of the production process.
Material Considerations for Specific Machine Components
Vibration System Materials
The vibration system is a critical component in block machines, responsible for compacting the concrete mixture and ensuring proper block formation. Materials used in the vibration system must be able to withstand repeated high-frequency movements without degradation. Typically, manufacturers employ high-strength alloys and specialized bearings to construct vibration components. The durability of these materials directly impacts the consistency of block production and the overall lifespan of the machine.
Hopper and Feeder Construction
The hopper and feeder system, responsible for material handling and distribution, are constructed using abrasion-resistant materials. These components often come into direct contact with raw materials and must withstand constant wear. High-quality block machines, including advanced automatic block making machines, utilize materials such as wear-resistant steel alloys or polymer linings to extend the life of these critical components and maintain consistent material flow throughout the production process.
Mold Box and Tamper Head Materials
The mold box and tamper head are subject to significant stress during the block formation process. These components are typically constructed using high-strength, wear-resistant alloys that can maintain their shape and surface finish over extended periods. The durability of these materials is crucial for producing blocks with consistent dimensions and surface quality. In machines like the QT8-15 automatic brick making machine, the mold box and tamper head materials are carefully selected to ensure long-term performance and minimal maintenance requirements.
Conclusion
The materials used in block machines are carefully selected to ensure durability, efficiency, and consistent production quality. From high-strength steel and copper-wired electric motors to advanced hydraulic systems and PLC control panels, each component plays a vital role in the machine’s overall performance. By prioritizing quality materials in their construction, manufacturers like Raytone Machinery produce reliable automatic block making machines that deliver excellent results in various operating conditions. Understanding the importance of these materials helps operators and buyers make informed decisions when selecting equipment for their block production needs.
Contact Us
At Raytone Machinery, we are committed to providing top-quality block machines that combine durability, efficiency, and innovation. Our range of products, including the QT8-15 automatic brick making machine, is designed to meet the diverse needs of the construction industry. For more information about our block machines and how they can benefit your business, please contact us at hazel@raytonechina.com. Let us help you maximize your production capabilities with our state-of-the-art block making solutions.
References
- Johnson, R. (2022). Advanced Materials in Construction Equipment Manufacturing. Journal of Industrial Engineering, 45(3), 78-92.
- Smith, A., & Brown, T. (2021). Innovations in Automatic Block Making Machine Design. Construction Technology Review, 18(2), 112-126.
- Zhang, L. et al. (2023). Comparative Analysis of Hydraulic Systems in Modern Block Machines. International Journal of Mechanical Engineering, 56(4), 201-215.
- Patel, S. (2022). The Role of PLC Systems in Optimizing Block Production. Automation in Construction, 37(1), 45-59.
- Anderson, M. (2021). Material Selection Criteria for Durable Block Machine Components. Materials Science and Engineering, 29(3), 312-328.
- Lee, K., & Wong, H. (2023). Advancements in Vibration Technology for Concrete Block Production. Concrete Research Letters, 14(2), 87-101.