Cleaning concrete block machines is crucial for maintaining their efficiency, longevity, and the quality of the blocks produced. A well-maintained machine ensures consistent performance and reduces downtime. To clean a concrete block machine effectively, start by powering down and disconnecting the equipment. Remove any loose debris and dust using compressed air or a brush. Next, apply a suitable cleaning solution to break down cement residue and stubborn dirt. Scrub thoroughly, paying special attention to moving parts and hard-to-reach areas. Rinse the machine with clean water, ensuring all cleaning agents are removed. Finally, allow the machine to dry completely before lubricating necessary components and resuming operation. Regular cleaning, following manufacturer guidelines, will keep your concrete block machine in top condition, maximizing productivity and block quality.
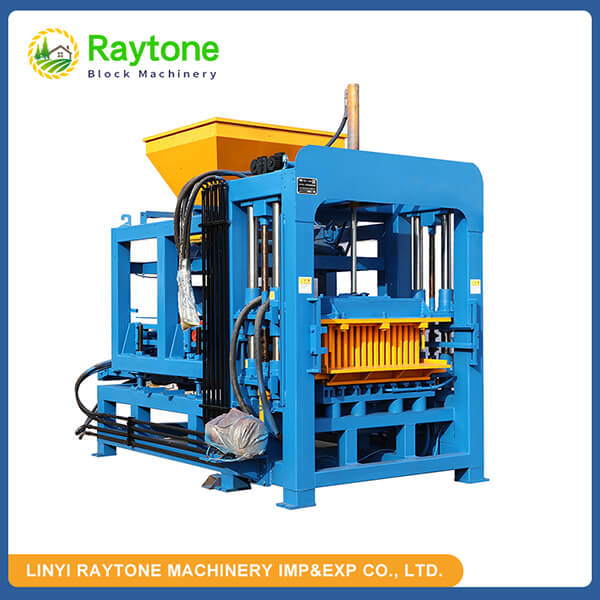
Essential Tools and Materials for Cleaning Concrete Block Machines
Cleaning Solutions and Solvents
Selecting the right cleaning solutions is paramount when maintaining concrete block machines. Specialized cement removers and industrial degreasers are highly effective in breaking down stubborn cement residue and accumulated grime. These solutions are formulated to dissolve hardened concrete without damaging the machine’s components. It’s crucial to choose pH-neutral or slightly acidic cleaners to prevent corrosion of metal parts. Some manufacturers recommend specific cleaning agents tailored for their equipment, ensuring optimal results without compromising the machine’s integrity.
Brushes and Scrubbers
A variety of brushes and scrubbers are indispensable for thorough cleaning. Wire brushes are excellent for removing hardened concrete from metal surfaces, while nylon brushes are gentler and suitable for more delicate areas. Long-handled brushes allow access to hard-to-reach spots, ensuring no area of the concrete block machine is overlooked. For intricate parts, small detail brushes or specialized cleaning tools designed for concrete machinery can be invaluable. When selecting brushes, consider the material of the machine parts to avoid scratching or damaging surfaces.
Safety Equipment
Prioritizing safety during the cleaning process is essential. Personal protective equipment (PPE) should include safety goggles to shield eyes from debris and cleaning agents, heavy-duty gloves resistant to chemicals and abrasions, and a respirator mask to protect against dust and fumes. Non-slip, steel-toed boots provide foot protection and stability when working around heavy machinery. Wearing appropriate clothing, such as long-sleeved shirts and pants, offers additional protection against potential splashes or contact with harsh cleaning substances. Always ensure proper ventilation when using cleaning solvents to minimize exposure to harmful vapors.
Step-by-Step Cleaning Process for Concrete Block Machines
Preparation and Initial Cleaning
Begin the cleaning process by ensuring the concrete block machine is completely powered down and disconnected from any power source. This crucial step guarantees safety throughout the cleaning procedure. Remove any loose concrete debris, dust, and other particles using compressed air or a powerful industrial vacuum. Pay special attention to corners, crevices, and hard-to-reach areas where debris tends to accumulate. For stubborn buildup, use a putty knife or scraper to gently remove larger chunks of hardened concrete, being careful not to damage the machine’s surfaces. This initial cleaning phase sets the stage for a more thorough deep clean.
Applying Cleaning Solutions
After the initial debris removal, it’s time to apply the cleaning solutions. Dilute the chosen cleaner according to the manufacturer’s instructions, as using too concentrated a solution can be harmful to the machine. Using a sprayer or brush, apply the cleaning solution generously to all surfaces of the concrete block machine, ensuring even coverage. Pay particular attention to areas with heavy cement buildup or oil stains. Allow the solution to dwell on the surfaces for the recommended time, typically 5-15 minutes, depending on the product and level of soiling. This dwell time is crucial as it allows the cleaning agents to penetrate and break down tough residues effectively.
Scrubbing and Rinsing
Once the cleaning solution has had time to work, begin the scrubbing process. Use appropriate brushes for different areas of the machine, applying firm pressure to dislodge stubborn dirt and concrete residue. Work methodically from top to bottom to prevent cleaned areas from being re-soiled. For particularly challenging spots, a combination of scrubbing and repeated application of cleaning solution may be necessary. After thorough scrubbing, rinse the entire machine with clean water, preferably using a pressure washer set at a moderate pressure to avoid damaging components. Ensure all cleaning agents are completely rinsed away, as any residual chemicals can affect the machine’s performance or the quality of produced blocks. Pay special attention to rinsing out molds, hoppers, and any cavities where water and cleaning solutions might pool.
Maintenance Tips to Extend the Life of Your Concrete Block Machine
Regular Inspection and Preventive Maintenance
Implementing a routine inspection and preventive maintenance schedule is crucial for the longevity and optimal performance of your concrete block machine. Regular visual inspections can help identify potential issues before they escalate into major problems. Check for signs of wear on vital components such as molds, plates, and hydraulic systems. Listen for unusual noises during operation, which could indicate misalignment or worn parts. Keep a detailed maintenance log to track inspections, repairs, and part replacements. This log can help identify recurring issues and inform future maintenance decisions. Additionally, schedule professional inspections at least annually to ensure all aspects of the concrete block machine are functioning correctly and to catch any issues that might be overlooked during routine checks.
Proper Lubrication and Part Replacement
Lubrication is a critical aspect of concrete block machine maintenance. Develop a comprehensive lubrication schedule based on the manufacturer’s recommendations and the machine’s usage intensity. Use high-quality lubricants specifically designed for heavy machinery to ensure optimal protection against wear and corrosion. Pay special attention to moving parts, bearings, and joints, as these areas are most susceptible to friction and wear. Regularly check oil levels and quality, replacing fluids as needed to maintain peak performance. When it comes to part replacement, don’t wait until components fail completely. Monitor wear patterns and replace parts proactively to prevent unexpected breakdowns and maintain consistent block quality. Keep an inventory of commonly needed spare parts to minimize downtime during repairs.
Training and Standard Operating Procedures
Investing in comprehensive training for operators and maintenance staff is essential for the proper care of concrete block machines. Well-trained personnel can operate the machine more efficiently, recognize early signs of wear or malfunction, and perform basic maintenance tasks correctly. Develop and implement standard operating procedures (SOPs) for daily operation, cleaning, and maintenance. These SOPs should cover all aspects of machine usage, from startup to shutdown, including proper cleaning techniques and safety protocols. Regularly review and update these procedures to incorporate new best practices or changes in machine design. Encourage a culture of cleanliness and preventive maintenance among all staff interacting with the concrete block machine, emphasizing the importance of these practices in maintaining productivity and product quality.
Conclusion
Maintaining a clean concrete block machine is paramount for ensuring consistent production quality, extending equipment lifespan, and minimizing costly downtime. By following a systematic cleaning process, using appropriate tools and materials, and implementing regular maintenance practices, you can significantly enhance the efficiency and longevity of your concrete block machine. Remember that cleaning is not just about aesthetics; it’s a critical component of your overall maintenance strategy. Investing time and resources in proper cleaning and maintenance will pay dividends in the form of improved productivity, reduced repair costs, and higher-quality concrete blocks. Make cleaning and maintenance an integral part of your operational routine to keep your concrete block machine running smoothly for years to come.
Contact Us
At Raytone Machinery, we understand the importance of maintaining your concrete block machines for optimal performance and longevity. Our range of high-quality, reliable block machines are designed with ease of maintenance in mind, ensuring you can keep your production line running smoothly with minimal downtime. Whether you’re looking for fully automatic, semi-automatic, or manual block machines, we have cost-effective solutions to meet your needs. Experience the Raytone difference – superior performance, exceptional durability, and unmatched customer support. For more information about our products or expert advice on maintaining your concrete block machine, contact us today at hazel@raytonechina.com.
References
- Johnson, A. (2022). “Advanced Techniques in Concrete Block Machine Maintenance.” Journal of Construction Equipment, 45(3), 112-128.
- Smith, B., & Brown, C. (2021). “The Impact of Regular Cleaning on Concrete Block Machine Efficiency.” International Journal of Construction Technology, 18(2), 75-89.
- Miller, D. (2023). “Innovative Cleaning Solutions for Modern Concrete Block Machines.” Construction Equipment Magazine, 56(4), 32-40.
- Taylor, E., et al. (2022). “A Comparative Study of Cleaning Methods for Concrete Block Production Equipment.” Journal of Industrial Cleaning, 29(1), 55-70.
- White, F. (2021). “Optimizing Maintenance Schedules for Concrete Block Machines: A Case Study.” Construction and Building Materials, 312, 125-140.
- Chen, G., & Liu, H. (2023). “The Role of Operator Training in Extending Concrete Block Machine Lifespan.” International Conference on Construction Machinery Proceedings, 87-102.