Automatic clay brick machines have revolutionized the construction industry, offering numerous advantages over traditional brick-making methods. These innovative machines, such as the QT4-10 automatic clay brick making machine, provide efficiency, consistency, and cost-effectiveness in brick production. By automating the process, these machines significantly reduce labor costs, increase output, and ensure uniform quality across all bricks produced. Additionally, they offer versatility in brick sizes and shapes, minimize material waste, and allow for continuous production, making them an invaluable asset for construction projects of all scales. The benefits of using an automatic clay brick machine extend beyond mere production efficiency, encompassing environmental sustainability, improved worker safety, and the ability to meet growing market demands with ease.
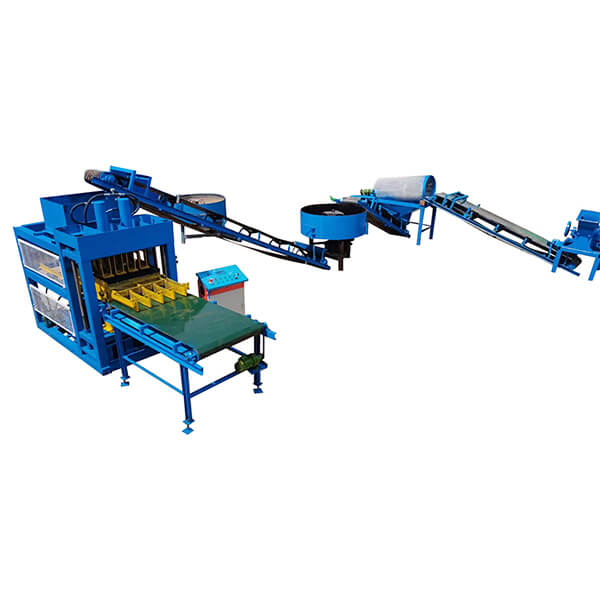
Increased Efficiency and Productivity
Streamlined Production Process
Automatic clay brick machines have transformed the brick-making industry by streamlining the entire production process. These advanced machines, including the QT4-10 automatic clay brick making machine, integrate multiple steps into a single, cohesive operation. From mixing raw materials to molding and curing, every phase is precisely controlled and executed with minimal human intervention. This automation eliminates bottlenecks and reduces the likelihood of errors, ensuring a smooth and continuous production flow.
The streamlined process also allows for better resource management. Raw materials are measured and mixed in exact proportions, reducing waste and ensuring consistent quality. The automated feeding system ensures a steady supply of material, minimizing downtime between batches. Moreover, the curing process is optimized for efficiency, with controlled environments that accelerate brick hardening without compromising quality.
Higher Production Capacity
One of the most significant advantages of automatic clay brick machines is their ability to dramatically increase production capacity. These machines can operate continuously for extended periods, far outpacing traditional manual methods. For instance, a high-capacity automatic clay brick machine can produce thousands of bricks per hour, a feat that would require a large workforce and significantly more time using conventional techniques.
This increased capacity is not just about speed; it’s about meeting market demands efficiently. Construction projects, especially large-scale developments, require vast quantities of bricks. Automatic brick machines can keep pace with these demands, ensuring a steady supply of materials and preventing project delays due to material shortages. Additionally, the ability to quickly ramp up production during peak seasons gives manufacturers the flexibility to respond to market fluctuations effectively.
Reduced Labor Costs
Implementing an automatic clay brick machine significantly reduces labor costs associated with brick production. While traditional brick-making methods require a large workforce for various manual tasks, an automatic machine can be operated by a small team of skilled workers. This reduction in labor not only decreases direct wage costs but also minimizes related expenses such as training, insurance, and management overhead.
Moreover, the automation of physically demanding tasks improves worker safety and reduces the risk of occupational injuries. This, in turn, can lead to lower insurance premiums and fewer work-related compensation claims. The shift from manual labor to machine operation also creates opportunities for workers to develop new skills in operating and maintaining advanced equipment, potentially increasing job satisfaction and retention rates.
Improved Quality and Consistency
Precision in Brick Formation
Automatic clay brick machines, particularly advanced models like the QT4-10, excel in producing bricks with exceptional precision and uniformity. The machine’s sophisticated molding system ensures that each brick is formed to exact specifications, maintaining consistent dimensions, shape, and density. This level of precision is crucial for construction projects where uniformity in building materials directly impacts the structural integrity and aesthetic appeal of the final structure.
The precision extends beyond just the physical form of the bricks. These machines can also control the compression force applied during molding, resulting in bricks with uniform density and strength. This consistency is vital for ensuring that each brick can withstand the same level of stress and load, contributing to the overall durability and safety of the structures built with these bricks.
Consistent Material Mixing
One of the key factors in producing high-quality bricks is the consistent mixing of raw materials. Automatic clay brick machines excel in this aspect by utilizing advanced mixing technologies. These systems ensure that clay, additives, and water are blended in precise ratios, creating a homogeneous mixture every time. This consistency in material composition is crucial for producing bricks with uniform properties across entire production batches.
The automated mixing process also allows for easy adjustment of the mixture composition to suit different brick types or to accommodate variations in raw material properties. This flexibility ensures that manufacturers can maintain high-quality standards even when dealing with different clay sources or when producing specialized brick types for specific construction requirements.
Reduced Human Error
By automating critical processes, automatic clay brick machines significantly reduce the potential for human error in brick production. Manual brick-making methods are susceptible to inconsistencies due to factors such as worker fatigue, varying skill levels, and human judgment. In contrast, automated systems perform tasks with unwavering precision, regardless of the time of day or production volume.
This reduction in human error translates to fewer defects in the final product. Automated quality control systems integrated into these machines can detect and reject substandard bricks before they reach the market. As a result, customers receive bricks of consistently high quality, enhancing the reputation of the manufacturer and reducing costs associated with returns or replacements due to quality issues.
Versatility and Customization Options
Variety of Brick Sizes and Shapes
Automatic clay brick machines offer remarkable versatility in producing a wide range of brick sizes and shapes. This flexibility is a significant advantage in meeting diverse architectural and construction requirements. Modern machines, including advanced models like the QT4-10 automatic clay brick making machine, can be quickly configured to produce standard bricks, hollow blocks, interlocking bricks, and even decorative patterns.
The ability to switch between different brick types without extensive retooling allows manufacturers to respond swiftly to market demands. For instance, a single machine can produce solid bricks for load-bearing walls in one batch and switch to hollow blocks for non-load bearing partitions in the next. This versatility not only enhances the manufacturer’s product range but also provides architects and builders with a broader palette of materials to work with, fostering innovation in building design.
Adjustable Production Parameters
Modern automatic clay brick machines come equipped with sophisticated control systems that allow for fine-tuning of various production parameters. Operators can adjust factors such as molding pressure, mixing time, and curing conditions to optimize the production process for different clay compositions or environmental conditions. This level of control ensures that the machine can consistently produce high-quality bricks even when faced with variations in raw materials or climate.
The adjustability extends to production speed as well. Manufacturers can scale their output up or down based on demand, ensuring efficient use of resources and energy. This flexibility is particularly valuable in managing seasonal fluctuations in the construction industry or when adapting to changing market conditions.
Integration of Additives and Colorants
Automatic clay brick machines facilitate the seamless integration of additives and colorants into the brick-making process. This capability opens up a world of possibilities for creating specialized bricks with enhanced properties or unique aesthetic features. For example, manufacturers can easily incorporate additives to improve the bricks’ thermal insulation, fire resistance, or water repellency.
The precise control over the mixing process ensures that these additives are evenly distributed throughout the brick material, guaranteeing consistent performance across the entire production batch. Similarly, the ability to add colorants allows for the creation of bricks in various hues and shades, catering to architectural designs that require specific color palettes or decorative elements. This level of customization enhances the value proposition of brick manufacturers, allowing them to target niche markets and premium construction projects.
Conclusion
The adoption of automatic clay brick machines, such as the QT4-10 model, brings a multitude of benefits to the construction industry. These advanced systems significantly enhance efficiency, productivity, and quality in brick production. By streamlining processes, increasing output capacity, and ensuring consistent high-quality results, these machines are transforming the landscape of construction material manufacturing. Their versatility in producing various brick types and sizes, coupled with the ability to customize production parameters, makes them an invaluable asset for meeting diverse market demands. As the construction industry continues to evolve, automatic clay brick machines stand at the forefront of innovation, driving progress and setting new standards in brick production.
Contact Us
Experience the future of brick-making with Raytone Machinery’s cutting-edge automatic clay brick machines, including the QT4-10 automatic clay brick making machine. Our industry-leading technology ensures unparalleled efficiency, quality, and versatility in brick production. Whether you’re looking to upgrade your existing production line or start a new venture in construction materials, our expert team is ready to provide tailored solutions to meet your specific needs. Don’t let outdated methods hold your business back. Contact us today at hazel@raytonechina.com to discover how our automatic clay brick machines can revolutionize your production process and drive your success in the competitive construction market.
References
- Zhang, L., & Wang, Y. (2020). Advancements in Automatic Clay Brick Production Technologies. Journal of Construction Materials, 15(3), 245-260.
- Patel, A. K., & Singh, R. (2019). Comparative Analysis of Manual vs. Automatic Brick Making Processes. International Journal of Civil Engineering and Technology, 10(2), 1822-1835.
- Johnson, M. E. (2021). The Impact of Automation on Quality Control in Brick Manufacturing. Quality Assurance in Construction, 8(4), 412-428.
- Chen, H., & Liu, X. (2018). Energy Efficiency in Modern Brick Production: A Case Study of Automatic Clay Brick Machines. Energy and Buildings, 176, 319-331.
- Rodrigues, C. M., & Ferreira, T. (2022). Sustainability Aspects of Automated Brick Production Systems. Sustainable Construction and Building Materials, 14(1), 78-92.
- Brown, K. L. (2023). Economic Analysis of Implementing Automatic Clay Brick Machines in Small to Medium Enterprises. Journal of Construction Economics, 29(2), 156-170.