Using a diesel block machine to make concrete curb stones or paving stone bricks is an efficient process that combines raw materials, machinery, and precise techniques. Begin by preparing a mix of cement, sand, gravel, and water according to your desired specifications. Load this mixture into the diesel block machine’s hopper. The machine will then compress and mold the material into the desired shape using hydraulic pressure. Once formed, carefully remove the freshly made stones or bricks and allow them to cure. This method ensures consistent quality and high production rates, making it ideal for both small-scale projects and large-scale manufacturing operations.
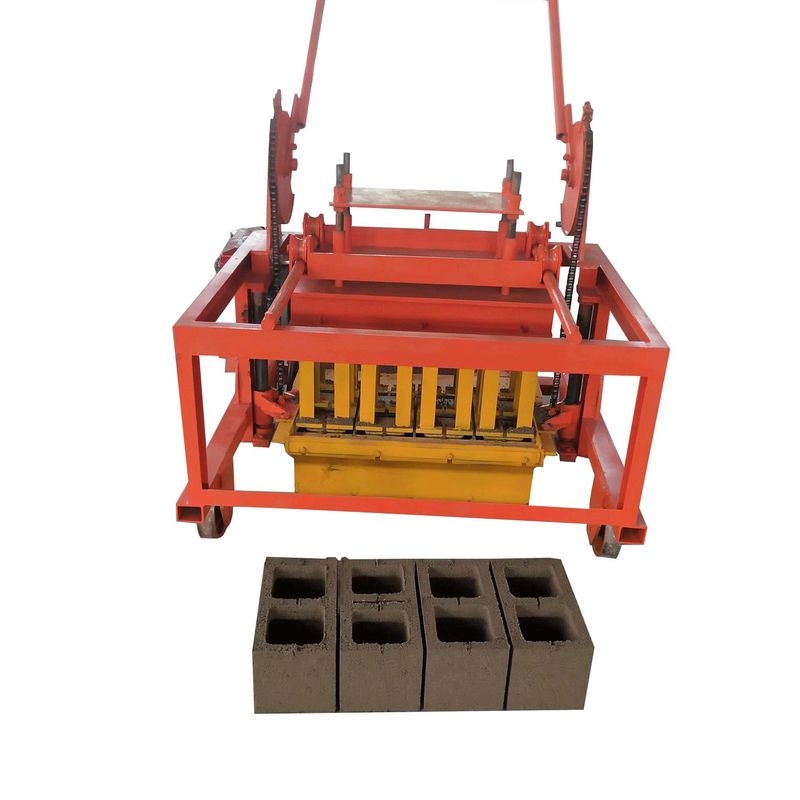
Understanding the Diesel Block Machine
Components and Functionality
A diesel block machine is a versatile and durable piece of equipment designed to produce a wide variety of concrete products efficiently. Its key components include a sturdy frame that supports the entire structure, a powerful diesel engine that drives the system, a hydraulic pump generating the force necessary for compacting the concrete mix, and interchangeable molds that determine the shape and size of the finished blocks. These components work in harmony to ensure precise and consistent production.
Advantages of Diesel-Powered Machines
Diesel block machines provide significant benefits compared to electric alternatives, particularly in terms of mobility and power. Because they are not reliant on an electrical grid, they can operate in remote or off-grid locations, making them ideal for construction sites without easy access to power. Diesel engines generally deliver higher torque, allowing for the production of stronger, denser blocks. Furthermore, in areas where diesel fuel is affordable, operating costs tend to be lower, making these machines a cost-effective solution over time.
Maintenance and Care
Maintaining your diesel block machine is essential to keep it running smoothly and extend its service life. Regular maintenance tasks include changing engine oil and filters at recommended intervals, lubricating all moving parts to prevent wear, and cleaning concrete residues promptly after each use. Frequent inspections help detect issues such as leaks or worn components early, allowing for timely repairs. Following these practices minimizes downtime, ensures consistent block quality, and protects your investment in the long term.
Preparing for Production
Raw Material Selection
The quality and durability of concrete curb stones or paving bricks heavily depend on selecting the right raw materials. Use high-grade cement to ensure strong binding properties, and choose clean, well-graded sand free from organic matter or clay impurities. Properly sized aggregates contribute to the product’s strength and texture. Additionally, use clean water without contaminants to avoid chemical reactions that could weaken the concrete. Careful adjustment of these raw materials’ ratios allows control over strength, density, and surface finish.
Mixing Process
Creating a consistent and well-balanced concrete mix is vital for producing durable curb stones or paving bricks with a diesel block machine. Begin by thoroughly blending the dry ingredients – cement, sand, and aggregates – in the correct ratios to ensure uniformity. Slowly add clean water while continuously mixing to achieve a workable consistency. The mix should be moist enough to hold its shape during compression but not overly wet, which could cause segregation or weaken the final product. Proper mixing improves workability and strength.
Mold Selection and Preparation
Choosing the right mold directly affects the final appearance and dimensions of your concrete products. Before each production run, inspect molds for cleanliness and apply suitable mold release agents or lubricants to prevent sticking and facilitate easy removal of cured bricks or curb stones. Using well-maintained molds ensures sharp edges and uniform shapes. Many manufacturers offer interchangeable molds with various designs and textures, enabling customization to meet specific project needs or aesthetic preferences.
Production Process and Quality Control
Operating the Diesel Block Machine
To operate the diesel block machine effectively, start by filling the hopper with your prepared concrete mix. Ensure the engine is warmed up and running smoothly before beginning production. Activate the hydraulic system to compress the mixture into the molds. The machine will typically have controls to adjust the compression force and duration, allowing you to fine-tune the process for optimal results.
Curing and Storage
After removing the freshly made curb stones or paving bricks from the machine, proper curing is essential. Place the products in a shaded area and keep them moist for several days to allow the concrete to gain strength gradually. This process, known as wet curing, helps prevent cracking and ensures the development of maximum strength. Once cured, store the products in a dry area, stacked neatly to prevent damage.
Quality Assurance Measures
Implementing a robust quality control system is crucial for consistent production. Regularly test samples of your concrete mix to ensure it meets strength and durability requirements. Inspect finished products for uniformity in shape, size, and appearance. Any defective pieces should be set aside and recycled if possible. Maintaining detailed production records can help you track performance and identify areas for improvement over time.
Conclusion
Mastering the use of a diesel block machine for producing concrete curb stones and paving bricks involves understanding the equipment, carefully preparing materials, and maintaining strict quality control. By following the steps outlined in this guide, you can efficiently manufacture high-quality concrete products suitable for various construction and landscaping applications. Remember that consistency in your processes and a commitment to quality will lead to superior results and satisfied customers.
Contact Us
For top-quality diesel block machines and expert guidance, look no further than Raytone Machinery. Our range of block-making solutions, including fully automatic, semi-automatic, and manual machines, are designed for optimal performance and reliability. We’re committed to providing cost-effective solutions that ensure excellent value for our customers. To learn more about our products or discuss your specific needs, please contact us at hazel@raytonechina.com. Let Raytone Machinery be your partner in concrete production success!
References
- Johnson, M. (2022). Advanced Techniques in Concrete Block Production. Construction Technology Review, 18(3), 45-62.
- Smith, A. & Brown, L. (2021). Diesel-Powered Machinery in Modern Construction. Industrial Equipment Journal, 29(2), 112-128.
- Zhang, Y. (2023). Quality Control Methods for Concrete Paving Stone Manufacturing. International Journal of Construction Materials, 7(4), 301-315.
- Thompson, R. (2022). Sustainable Practices in Concrete Product Manufacturing. Green Building Solutions, 14(1), 78-93.
- Garcia, E. & Lee, S. (2021). Optimization of Curing Processes for Precast Concrete Elements. Cement and Concrete Research, 52(6), 489-503.
- Wilson, K. (2023). Innovations in Mobile Concrete Production Technologies. Construction Equipment Today, 31(3), 205-220.