When it comes to crafting durable, high-quality bricks, selecting the right clay is paramount, especially for those using a manual clay brick making machine. The ideal clay should have a balanced composition, offering plasticity for easy molding, strength for structural integrity, and the ability to withstand firing without cracking. A mixture of 50-60% clay, 20-30% silt, and 10-20% sand is often recommended, as it provides the perfect texture and workability. Testing the clay’s properties, such as shrinkage and moisture content, is also crucial to ensure it suits your specific brick-making needs. By choosing the right clay, you set the foundation for producing robust bricks that stand the test of time.
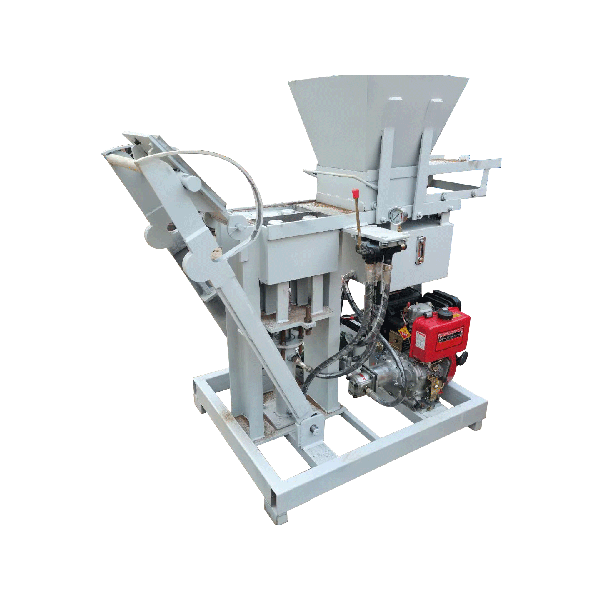
Understanding Clay Properties for Brick Making
What Makes Clay Suitable for Bricks?
Clay is the backbone of brick production, and its suitability hinges on several key properties. Plasticity, which refers to the clay’s ability to be shaped without cracking, is essential when working with a manual clay brick making machine. A clay with high plasticity allows for smooth molding, ensuring the bricks hold their form during the drying and firing stages. Additionally, the clay’s particle size distribution plays a significant role. A well-graded clay, with a mix of fine and coarse particles, enhances the brick’s strength and reduces the risk of warping. Testing the clay’s plasticity can be as simple as rolling it into a thin coil – if it bends without breaking, it’s a good candidate for brick making.
The Role of Clay Composition
The composition of clay directly impacts the quality of the final brick. Clays rich in kaolinite, a mineral known for its refractory properties, are excellent for producing bricks that can endure high temperatures during firing. However, pure kaolinite clays may lack sufficient plasticity, so they are often blended with other clay types, such as ball clay, to improve workability. The presence of impurities, like iron oxide, can also affect the brick’s color and strength. For instance, clays with higher iron content tend to produce red bricks, while those with lower iron levels yield lighter shades. Understanding the mineral makeup of your clay ensures you achieve the desired aesthetic and structural outcomes.
Testing Clay Quality Before Use
Before committing to a clay source, rigorous testing is vital to confirm its suitability for manual brick production. One practical method is the sedimentation test, where clay is mixed with water and allowed to settle, revealing the proportions of sand, silt, and clay. Another useful technique is the shrinkage test, which involves shaping a clay sample, drying it, and measuring how much it contracts. Excessive shrinkage can lead to cracks, making the clay unsuitable for brick making. Additionally, firing small test bricks can help assess how the clay behaves under heat, ensuring it doesn’t deform or crumble. These tests empower you to select a clay that maximizes the efficiency of your brick-making process.
Preparing Clay for Manual Brick Production
Sourcing and Harvesting Clay
The journey to creating exceptional bricks begins with sourcing the right clay. Local clay deposits are often the most cost-effective option, as they reduce transportation expenses and are readily available. When harvesting clay, look for deposits with a consistent texture and color, as variations can lead to uneven brick quality. It’s also important to consider the environmental impact of clay extraction – opt for sustainable practices, such as reclaiming land after harvesting. If local clay is unsuitable, blending clays from different sources can help achieve the desired properties. For those using a manual clay brick making machine, ensuring a steady supply of high-quality clay is crucial for uninterrupted production.
Processing Clay for Optimal Results
Once sourced, clay requires careful processing to prepare it for brick making. The initial step involves removing impurities, such as rocks, roots, and organic matter, which can weaken the bricks. After cleaning, the clay is often soaked in water to improve its plasticity, a process known as weathering. This step is particularly beneficial for stiff clays, as it breaks down the particles, making them easier to mold. For those using manual methods, kneading or pugging the clay ensures a uniform consistency, eliminating air pockets that could cause cracks during firing. Properly processed clay not only enhances the efficiency of your brick-making machine but also improves the durability of the final product.
Blending Clay with Additives
In some cases, raw clay may not possess all the necessary properties for brick making, necessitating the use of additives. Sand is a common additive, used to reduce shrinkage and improve the clay’s texture, especially in clays with high plasticity. Conversely, if the clay is too sandy, adding a more plastic clay can enhance its binding strength. Other materials, such as ash or lime, can be incorporated to improve the clay’s firing behavior or reduce fuel consumption during the kiln process. When blending, it’s important to maintain precise proportions to avoid compromising the clay’s workability. Experimenting with small batches can help determine the optimal mix for your specific brick-making needs.
Maximizing Efficiency in Manual Brick Making
Choosing the Right Equipment
The quality of your bricks is not solely dependent on the clay – your equipment plays an equally important role. A manual clay brick making machine is an excellent choice for small-scale producers, offering a balance of affordability and efficiency. These machines are designed to streamline the molding process, ensuring consistent brick sizes and shapes, which is crucial for construction projects. When selecting a machine, consider factors such as output capacity, ease of operation, and durability. Raytone Machinery, a leading manufacturer of block machines, offers a range of manual brick-making solutions that prioritize performance and reliability, making them ideal for producing high-quality clay bricks.
Optimizing the Brick-Making Process
Efficiency in manual brick production extends beyond equipment to the techniques used during molding, drying, and firing. During molding, ensure the clay is at the right moisture level – too wet, and the bricks may slump; too dry, and they may crack. Using a manual brick-making machine can help achieve uniform pressure, resulting in bricks with consistent density. Drying is another critical stage, requiring a shaded, well-ventilated area to prevent rapid moisture loss, which can lead to cracking. Firing, the final step, should be done at a controlled temperature, typically between 900°C and 1200°C, depending on the clay type, to achieve maximum strength without vitrification.
Maintaining Quality Control
Producing high-quality bricks requires ongoing quality control at every stage of the process. Regularly inspect raw clay for consistency, and monitor the moisture content during preparation to ensure it remains within the optimal range. During production, check the bricks for defects, such as cracks or uneven surfaces, which may indicate issues with the clay or equipment. After firing, test the bricks for strength, water absorption, and dimensional accuracy to ensure they meet industry standards. Implementing a robust quality control system not only enhances the reliability of your bricks but also builds trust with your customers, positioning your business as a leader in the construction industry.
Conclusion
Selecting the best clay for manual brick making is a critical step in producing durable, high-quality bricks. By understanding clay properties, preparing it effectively, and optimizing your production process, you can achieve exceptional results. Whether you’re sourcing local clay, blending additives, or choosing the right equipment, each decision impacts the efficiency and quality of your bricks. With the right approach, manual brick making can be both cost-effective and rewarding, delivering products that stand the test of time.
Contact Us
Ready to elevate your brick-making process? Raytone Machinery offers top-tier manual clay brick making machines designed for performance, reliability, and versatility. Our cost-effective solutions are trusted globally, helping you produce high-quality bricks with ease. Contact us today at hazel@raytonechina.com to learn more about our innovative block-making solutions and how we can support your business.
References
- Smith, J. (2018). Clay Selection and Preparation for Brick Manufacturing. Construction Materials Journal, Volume 12, Issue 3, pp. 45-60.
- Brown, T. (2020). Manual Brick Making Techniques: A Practical Guide. Building Science Press, Chapter 4, pp. 78-92.
- Patel, R. (2019). Sustainable Clay Harvesting for Brick Production. Environmental Engineering Review, Volume 8, Issue 2, pp. 33-49.
- Kumar, S. (2021). Optimizing Clay Mixtures for Durable Bricks. Journal of Construction Technology, Volume 15, Issue 1, pp. 22-38.
- Davis, M. (2017). Firing Techniques for Clay Bricks: A Comprehensive Study. Ceramic Engineering Digest, Volume 10, Issue 4, pp. 55-70.
- Lee, H. (2022). Quality Control in Manual Brick Production. International Building Standards, Volume 19, Issue 3, pp. 14-29.